Inspiration and helpful sources
A bit more than a year ago I bought a 3D printer because I really wanted to and argued with the idea that I'd like to build my own quadcopter at some point and would need it to print parts for it.
Inspired by first person view multicopter racing videos on youtube I did decide on some nice efficient and cheap motors at some point but didn't go through with buying anything.
Now the motors I selected back then are quite hard to come by so I decided to start the search for parts from scratch again.
Having no idea of anything related to this about 3 weeks ago it turned out that while all the information is out there some of it is quite scattered which is why I am documenting my steps here.
A good general introduction to get started is this article about multicopters.
I also got some useful advice from this forum thread.
This first part will mostly just put the key information of those two sources into one place based on my build and experiences so far.
General idea
I have no idea of hardware, electronics and soldering. Okay maybe I have some basic understanding, but it is very shallow. I am a programmer though, so using a ready to go flight board was out of question.
I already had the microcontroller of my choice and will introduce it here in a bit and write about the software in later parts of this series.
What I expect from my quadcopter is that it is exactly that, with 4 powerful motors and a size that fits my room for testing but big enough for an easy stable flight outside even if there is a tiny bit of wind.
I plan on adding a camera, want it to look kinda nice and most important: Be able to print the frame with my 3D printer. I also expect to break things, so things need to be easy to replace.
Since I don't want to get too deep into the electronics, I do need some presoldered parts.
The microcontroller
A quite expensive but powerful, low energy microcontroller which seems great for this is the Intel Edison which features a 500MHz dual core Atom CPU and a 100MHz Quark MCU (for hard realtime applications), 1GB RAM and on board WiFi and Bluetooth in a very small form factor and an energy consumption of <1W.
There are some arduino board for the Edison which would open a lot of possibilities but add a lot to the size. Fortunately Sparkfun has a line of small blocks made to interface with the Edison which can be stacked easily on top of each other adding functionality.
One of those blocks features powering it via USB, another one adds a 9DOF unit with gyroscope, accelerometer and magnetometer which will be required for stable hovering and flying and then there is a PWM block, which will be needed to talk to the speed controllers to get the motors to spin and I also attached a display block with some minimalistic buttons and a small OLED display.
I already had everything but the PWM block already, so this was an easy choice for me. My alternative would have been a Raspberry Pi because I got one of those too and with a much larger community there is a lot more information about it. But adding all the required hardware would probably have made this harder in terms of putting the electronics all together and would have ended up to be a lot bigger.
There are many other possible choices and there are also different plug and play flight boards for multicopters, which is what most people seem to use.
Cables
I just bought everything from Hobbyking and didn't waste any thoughts on the cables/plugs of the items. Mine fortunately all turned out to fit, but there are many different types and you should definately keep an eye on them. So the motor cables should fit the esc, and the esc cable needs to interface the battery and the microcontroller in some way. Sure you can just not use plugs between the parts, but that isn't really fun either. So you should make sure everything fits or get parts to make it fit.
The motors
The choice of motors is really big, but common for multicopters are brushless outrunner motors, which I believe means that they don't have a "brush" inside to make them spin by changing the electro magnets direction and also the elctro magnet does not rotate but instead the part around it which would be fixed in a "classical" motor. This reduces friction, improves reliability and makes it more reactive due to less mass being moved.
The disadvantage is that the motor on it's own does not rotate just by attaching a batterie to it. Instead it provides three cables and requires a microcontroller to do a job similar to what the "brush" would do for other motors.
These microcontrollers are called "Electronic Speed Controllers" or ESC in short. They will be attached to the motor, the battery and the flight board and use all that to control the rotation speed.
This already reduces the choice of motors significantly but it is still large. apparently you want a smaller, faster motor with a smaller propeller for fast and reactive controls on small multicopters, but bigger and slower motors with bigger propellers on bigger multicopters wich are easier to handle and have a much more stable flight.
The speed is usually given in "Kv" which is a constant for the motors RPM per Volt.
A Kv over 2000 seems to be really big and a Kv smaller than 600 is quite low, so most multicopters use something between that and around 1000 appears to be quite common for a multipurpose build.
Besides the speed, it is also important to take a look at the motors thrust data. It is usually given in form of a table or diagram showing test data of using the motors at different voltages with different propellers at different speeds and how big there power consumption will be in that configuration.
A good starting point for the thrust is that the complete multicopter should at least have a thrust of twice its mass. My guesstimate was that in the worst case my build would weight around 1.5kg which means that each of the four motors needs a thrust of 3kg/4 = 750g per motor or more.
I settled on the Multistar Elite 2312-KV980 in a pack of two one for clock wise rotation and one for counter clock wise, which usually is a matter of just switching two cables, but these are for threaded quick mount propellers. And while the correct rotation direction just keeps the propellers perfectly in place the other one would losen them and have them quite immediately fly away.
These motors have a Kv of 980 and a maximum thrust of 840g with 11.1V and will usually not need more then 10A + some spikes.
They cost about 17€ per motor.
I also got M3x8 hex screws to mount the motor to my frame with.
Propellers
I just went with the recommended ones from the dataset. Self tightening 9450 propellers. 9450 refers to the length in inch, which is 9.4inch and the pitch, also in inch which is the distance the propeller would travel through a solid (if it could) with a single rotation.
There are many others, but propellers are quite cheap and easy to replace, so I'll may or may not experiment with these at some later point.
Battery
Currently the best choice for batteries for pretty much everything seem to be Lithium-Polymer batteries. There are three important values: The voltage/cell count, the capacity and C rating.
Those batteries are made out of cells and in a standard LiPo battery one cell has an average voltage of about 3.7V. A so called 3 cell battery has three cells in sequence, resulting in a voltage of 11.1V. Bigger motors may need more than that, smaller ones may need less. You don't have to use the maximum supported voltage of a motor, but you shouldn't go higher than that.
Just use what according to the motor data seems like a good start. In my case that is a 3 cell battery.
The voltage of a full cell is around 4.2V and should not get lower than 3V (it can, but won't be good for the battery).
I got this small indicator which can be attached to a battery and will indicate if a cell is "too empty".
The capacity is important for the flight time, but a higher capacity also means a bigger battery with more weight, so more capacity can also cause a shorter flight time if it means that the motors have to run much faster just to generate enough thrust.
The capacity is given in Ah or mAh. So if the battery has a capacity of 4Ah, you can draw 4A for 1h until it is empty. Assuming my 4 motors would draw an average of 40A during the flight I could fly for 4Ah/40A = 0.1h = 6mins. Because that battery is already really big I hope that in reality the motors will draw less power on average...
The C rating was new to me and refers to the discharge rate of the battery. Because if the battery only allows you to draw 20A, but instead you keep drawing 40A all the time, bad things may happen. The C rating is some kind of multiplicator to the capacity. So if the 4Ah battery has a discharge rating of 25C, it means that it is okay to draw 25*4A(h) = 100A. Often the batteries have two C ratings like this: 25-50C discharge, where 25C is the power you can easily draw all the time, but if the are some peaks of up to 50C that won't immediately break the battery.
You should also keep an eye on weight and size.
I got two batteries. Both with 3 cells and 25-50C discharge and one big one with 4000mAh and a smaller one with 3300mAh.
I also got a distributor cable, branching each of the quite thick battery cables into 4 thinner ones fitting the ESCs.
Also a LiPo charger, but the included cables don't fit my batteries, so I am currently waiting for fitting ones.
Speed controllers
Apparently everything works for these. The ones running the open source SimonK firmware are supposed to be the best for multicopters but some other can be flashed with it. They do come with a current rating. So you shouldn't use a 10A ESC with a motor drawing 20A. It however is no problem to use a 30A ESC with a motor drawing just 10A.
I got 4 of the 30A Afro ESCs.
Conclusion
I took about two weeks for the parts to arrive from Hongkong. I ordered 6 instead of 4 motors and 5 instead of 4 ESCs as well as 4 additional propellers, in case something arrives broken or gets broken by me. So far it all works though :).
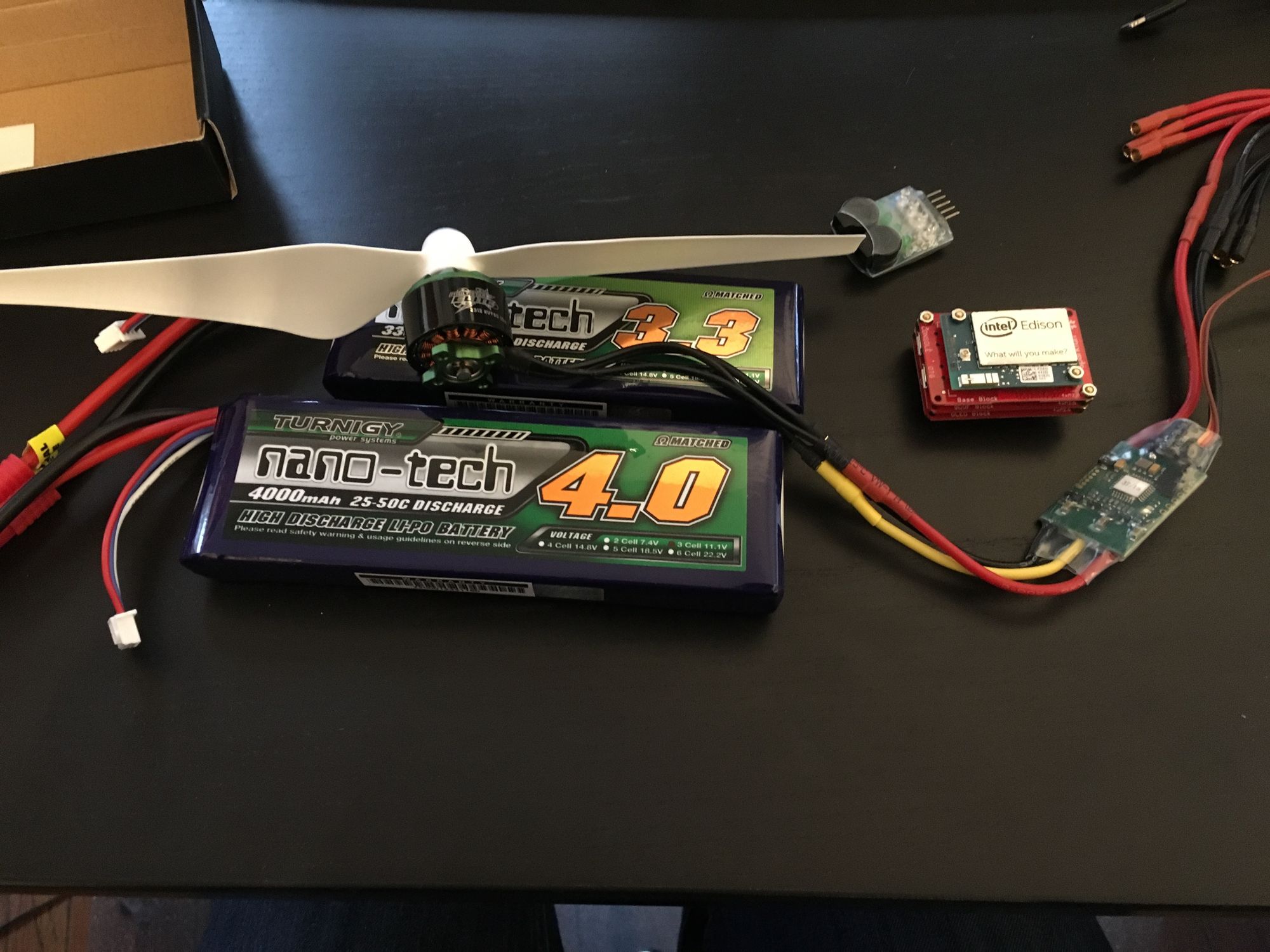